17 Reasons Why You Shouldn't Avoid Refrigerated Containers
Refrigerated Containers
Refrigerated Containers (also known as reefers) are used by a variety of industries to transport temperature-sensitive products over long distances. From catering companies that provide ready-to-eat meals to research labs that are transporting blood plasma, a refrigerated container can be customized with features such as remote monitoring and backup power options.
Using a refrigerated shipping container ensures that your products arrive in pristine condition. Modern refrigeration units focus on energy efficiency and high-quality insulation.
Customization
Every decision you make in regards to refrigerated container safety and integrity plays a role. From size variants that fit the needs of various shipping options to advanced features that enhance cold chain management, your discerning choices ensure that you have the best conditions for shipping needed to ensure that your products are at their peak.
If you select a container that matches the volume of your product, you will be able to minimize temperature fluctuations and maximize efficiency in energy use. The type of insulation you choose is crucial as well. Both vacuum and foam insulation panels are available, however the choice depends on your requirements. Foam is more affordable, but vacuum insulation panels have superior thermal resistance.
In the world of reefer technology using IoT capabilities allows for continuous monitoring and alerts to ensure your shipment is safe throughout its journey. Digital advancements also improve efficiency in operations and supply chain visibility.
A specialized refrigeration unit can be designed to meet the unique requirements of your products and ensure their safety on long trips for example, in the case of live cargo or pharmaceuticals. These containers may have redundant systems to avoid unexpected system failures. They may also be equipped with the latest materials that are compliant with the strict standards of the pharmaceutical industry or guarantee the safety and health of the transit environment for animals.
Other technical innovations may include airflow vents as well as fresh air ducts that control the atmosphere inside, keeping it in a stable state. These piping systems remove gases such as ethylene, which accelerates the ripening process of fruits and help ensure an uniform distribution of temperature throughout the container. A built-in drainage system stops the buildup of water and insects infestation.
Energy Efficiency
Refrigerated Containers provide a secure and safe place to store temperature-sensitive cargo. They can be used to protect food items, pharmaceuticals, premium foods and other items. They are made with advanced control systems and top-quality insulation to keep internal temperatures stable. They also come with enhanced security features to protect your products from vandalism and theft. Some containers are also designed to be eco-friendly and make use of renewable energy sources, which makes them a sustainable choice for companies.
While refrigeration systems are crucial to ensure the quality of cargo, they can consume significant amounts of energy. This is particularly the case when there are multiple containers stored on the same vessel or at a terminal. The high power consumption can be offset by using refrigerators equipped with automated temperature control systems. These systems monitor and adjust the container's temperature according to the environment around it which can result in substantial savings.
Modern refrigerated containers (reefers) that are designed to be energy efficient, use advanced cooling and insulation technologies in order to minimize the power consumption. They are also typically equipped with diesel generators, which are able to be used in areas without access to electrical power. This allows them to operate in the middle of the road or even when stationary power isn't available.
The heat exchange between the container interior and the surrounding environment is responsible for a significant portion of the energy consumption in refrigerated containers. This heat exchange occurs through the use of insulation that is cold-resistant. Its share ranges from 35 to 85% during cooling, and as high as 50 % when heating (Filina & Filin, 2004).
The following measures are recommended to cut down on the energy consumption by refrigerated container. These include adjusting the layout of the terminal and the use of electrical handling equipment as well as the search for energy-saving operations of refrigerated containers with cooled or frozen cargo, and the integration of truck scheduling and cranes (Yang and Lin 2013). Source Webpage is worth noting that the reduction in ( Overset bullet Q _1 The total energy consumption will be reduced in proportion by reducing the component share. As part of their innovation and energy-saving strategies for small seaports and container terminals are encouraged to adopt the proposed measures.
Security
Refrigerated containers have advanced security features that guard your items from being damaged by. The robust container's construction is able to withstand environmental damage and external temperature fluctuations, and the door locks are built-in to prevent unwanted unauthorized access. Furthermore the refrigeration systems are fully separated from the rest of the container to ensure that any tampering or malfunction does not affect the temperature control. The units can also come with temperature alarms that alert you to any problems in real-time.
Many industries depend on refrigerated containers for the transportation of their products. From catering companies that ship prepared meals to research laboratories that transport sensitive samples, refrigerated containers provide reliable, temperature-controlled transportation. Refrigerated containers not only preserve the quality of goods but also assist businesses reduce waste. Waste and sludge are a major problem in industries which deal with perishable items. Spoilage can cause financial losses, but also affect the safety of consumers. With advanced temperature control, refrigerated containers can preserve the quality of the products, increasing their shelf lifespan and making them available for longer.
The high-quality insulation found in refrigerated containers keeps the interior at a stable temperature, which allows for precise control of the inside environment. Modern reefer containers are capable of a range of cooling options, from chilled to subzero freezing. This allows you to tailor the temperature to meet your individual requirements and ensures that your products are in optimal condition.
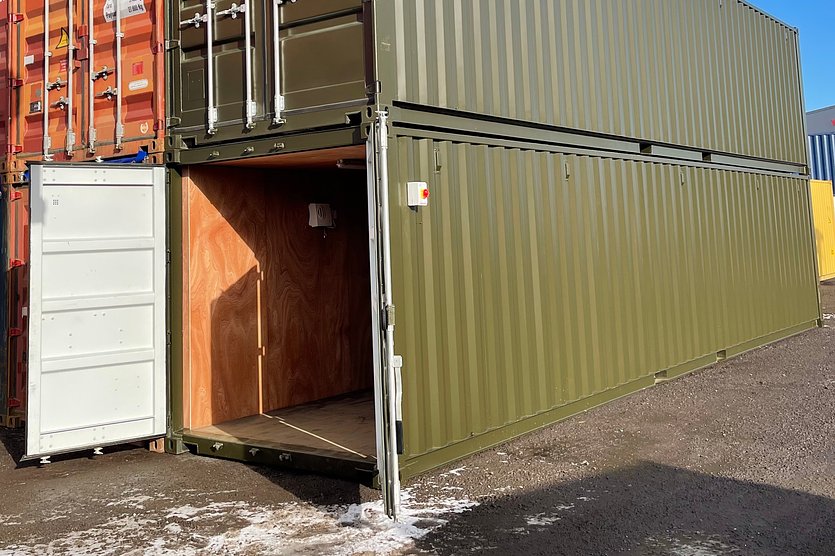
Additionally, premium refrigerated containers are equipped with advanced air circulation systems that ensure constant temperature throughout the cargo area. They are equipped with fans that distribute cold air evenly to avoid hot spots and provide superior airflow. The units are also fitted with humidity control, making sure that your product remains fresh and free from deterioration. Fruits and vegetables are especially sensitive to humidity control since they continue to produce heat and ethylene even after harvest. The ventilation system is designed to eliminate these gases.
Refrigerated containers are an essential part of global trade, allowing businesses to reach customers around the world without compromising product quality. To meet your needs, look for units with precise temperature controls, remote monitors and backup power options.
Maintenance
Refrigerated Containers are a great way to transport temperature-sensitive cargo, but they require proper maintenance and cleaning to ensure optimal performance. Some of the best ways to keep refrigerated containers in good condition include regular calibration and maintenance of the power, insulation maintenance, and door maintenance.
Monitoring of Temperature
Refrigerated Containers have the ability to monitor temperatures in the container remotely, ensuring that they stay within a set range throughout their journey. This feature also gives logistics professionals detailed logs of data for quality assurance purposes. Additionally, special reefer containers are equipped with back-up power sources to prevent interruptions to temperature control systems.
Cooling
Airflow systems are utilized in refrigerators to distribute cold air through the container, keeping the cargo at the optimal temperature. This helps to remove moisture, gases, and ethylene that are produced by vegetables and fruits which can cause spoilage.
It is essential to inspect regularly the insulated piping of reefers for leaks. Using an halide and soap lamp or electronic leak detector could assist in determining the source of any issue. It is also a good idea for you to inspect the inside of the refrigerator unit periodically for any signs of ice accumulation. This can affect the cooling capacity of the container and should be addressed as soon as possible.
A major element of the cooling process is the compressor, which is responsible for pressurizing and circulating the refrigerant within the refrigeration system. Performing routine calibrations of the compressor can increase efficiency and decrease energy consumption.
Insulation is a crucial component of special reefer containers, as it minimizes the heat exchange between the interior and exterior. Quality insulation materials such as polyurethane foam are utilized to maximize the efficiency of thermal energy and to maintain constant temperatures throughout the entire shipping journey.
The final step in maintaining the integrity of refrigerated containers is to perform regular cleanings. This involves cleaning the interior of the container and wiping off all surfaces. This is especially important in areas where the seals on doors could be damaged, like under and behind them.
It is also a good idea to re-paint the exterior of a refrigerated container regularly. Use marine-grade paint to shield the container from rust and keep it in perfect condition. It is also essential to repair minor scratches that may affect the integrity of seals.